Reduce and Recycle Waste
- Top
- Sustainability
- Materiality
- Reduce and Recycle Waste
We will build a system that prevents valuable resources from being wasted, via proper demand forecasting, inventory management, and business execution.
- Reduce the Amount of Waste
- Improve the Defect Rate by Improving Quality of Original Products
- Promote Reducing, Reusing, and Recycling
Reduce the Amount of Waste
The Happinet Group leverages the marketing function it has developed over the years to properly assess market trends and needs. Through this process, we promote accurate demand forecasting and proper inventory management in each business to reduce the amount of waste generated from products and promotional materials. We also comprehensively review our operations, aiming to build a business promotion system that avoids wasting valuable resources.
Reducing the Amount of Waste through Utilization of Data
In the Visual & Music Business, we reduce the amount of waste by coordinating with manufacturers on the required quantity of sales promotion materials, which we compile based on fluctuations in space used for sales promotions and demand trends, using this to optimize the production quantity of such materials.
In addition, we are also working to provide sample discs (CDs and DVDs) for stores in digital data form as much as possible to meet the needs of retailers and reduce the amount of waste.
In the Amusement Business, we have installed IoT systems in some capsule-toy vending machines, which are in operation all over Japan. These systems use sensors to detect the number of products sold per machine. The ability to manage data on sales trends and inventory status at stores equipped with these systems has led to more efficient inventory management, and has also contributed to streamlining operations for our sales teams, such as optimizing observation.
Streamlining and Refining Demand Forecasting with AI
For the Happinet Group, which handles trending merchandise, demand forecasting is an essential tool for ordering at the exact right quantity. However, manual demand forecasting requires a great deal of time to collect, process, and aggregate data in preparation for decision-making, and the forecasting process is dependent on the experience and intuition of the person handling the process.
That is why we utilize AI for demand forecasting, automatically collecting and processing not only past results, but also a wide range of other data, including customer reviews and information from social media, to create forecasting demand models for movies and toys. In addition, various decision factors that fall under the realm of tacit knowledge are also reflected in the AI model to improve forecast accuracy.
The ability to accurately forecast demand based on data not only reduces lost sales opportunities due to shortages and improves customer satisfaction, but also mitigates excess inventory, reduces waste, and reduces siloing as well as workload for those in charge of the process.
Making Efforts to Go Paperless in All Divisions
In the Toy Business, we are reducing the amount of faxes we send and receive by switching from fax to email for communication, such as when providing information to business partners, as well as when taking and placing orders. For clients for whom communication via fax is required, we utilize document handling software to edit, reply to faxes, and store documents on a PC, thereby improving productivity. In addition, we only print out paper for essential data, which significantly reduces the amount of paper used.
In the Visual & Music Business, we are making efforts to go paperless by coordinating with manufacturers to post information on new releases in PDF format online. We are also working to provide in-store promotional materials (posters, flyers, store POPs, etc.) in digital data form as much as possible to meet the needs of our customers.
Improve the Defect Rate by Improving Quality of Original Products
In addition to intermediate distribution, the Happinet Group’s business also includes planning and development of original products. We strive to improve the quality of these products to reduce the amount of waste caused by product defects.
Reducing the Defective Rate and Reducing Waste
In the Toy Business, we inspect any products that have defects and advise production plants on areas they can improve in the production process. We then verify the effectiveness of these improvements based on the rate of defective products.
By implementing a PDCA cycle of Analysis → Improvement → Production → Verification, we are making improvements to product quality and reducing waste.
Additionally, as a preliminary step to determining if a product is defective, we have created a set of product Q&As that we share with the customer service center. Through analysis of defective products, we realized that many were in fact caused by customers mishandling the product or not knowing how to use it properly. We therefore created a troubleshooting page (In Japanese only) on our website in February 2023 that summarizes the most common problems by product. Furthermore, by collaborating with and providing guidance to the customer service center regarding these issues, we are making customers who make inquiries feel more satisfied, while also helping to reduce product waste.
Promote Reducing, Reusing, and Recycling
The Happinet Group’s efforts extend beyond products. We also promote ongoing improvements in packaging materials for shipping and equipment for business operations, aiming to reduce their use and to use them more effectively.
Promoting the 3Rs
To minimize the use of cardboard in the logistics division, we are promoting shipping using reusable collapsible containers and stocking a wide variety of cardboard sizes to enable optimal packing of products based on quantities and their specific characteristics. We are also working to prevent the use of excess packaging materials, for example, by continually reviewing the shape and size of packaging according to the type of products shipped. In addition, our logistics division promotes the recycling of cardboard and other non-reusable materials.
We are also striving to reduce our amount of general waste, even with regard to small pieces of paper and plastics, conventionally difficult to recycle, by thoroughly separating them and delivering them to recycling businesses.
In addition, in the Amusement Business, when disposing of composite waste such as capsule toys and vending machines, half of this waste is used for thermal recycling and subsequently material recycling. A portion of the iron is also reused.
Furthermore, we are conducting research and verification on the recycling and reuse of empty capsules, which arise when capsule toys are sold. In the future, we plan to continue considering measures with manufacturers to reduce the impact that empty capsules have on the environment.
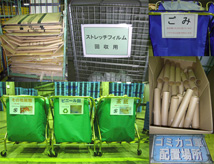
Review of Packaging Methods in Distribution
In the logistics division, we are striving to reduce the amount of packaging tape used and the associated CO2 emissions by taping boxes closed once down the middle and once across, rather than down the middle and at both ends. Furthermore, we aim to further reduce CO2 emissions by testing environmentally friendly paperbased and biomass-based oriented polypropylene (OPP) tapes.
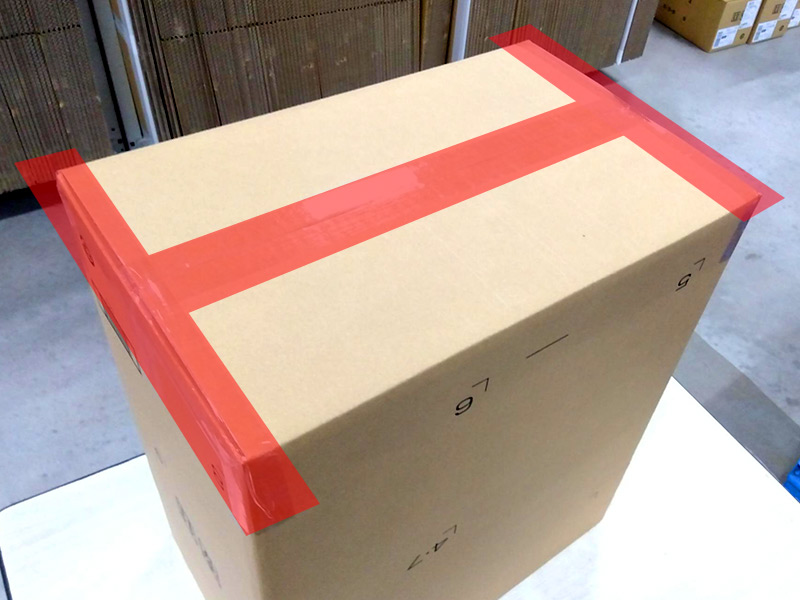
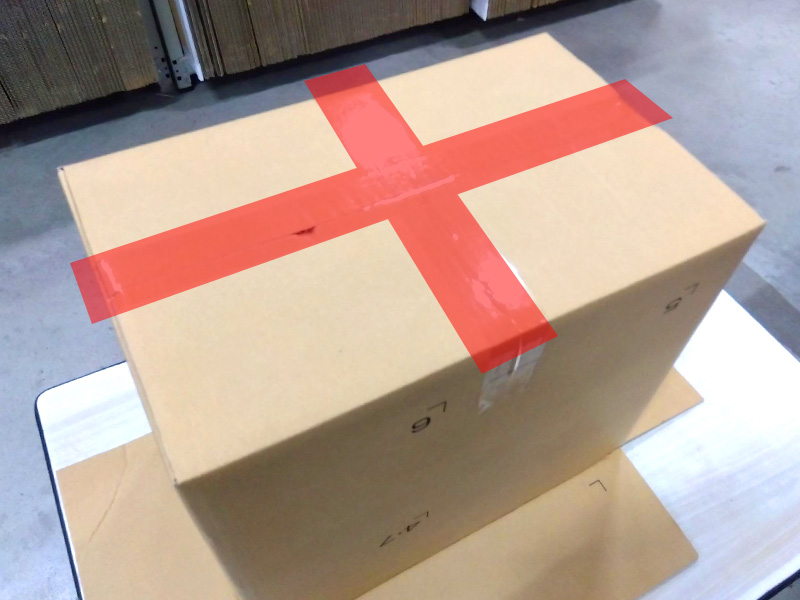